

- #Simatic step 7 speed calculation block how to
- #Simatic step 7 speed calculation block verification
- #Simatic step 7 speed calculation block software
In addition, the model provides an option to simulate a sensor error with the elements failureSensorB1 and failureSensorB2. When the box reaches one of the sensors, the value at the sensor output is set from 0 to 1. End position sensors are located at both ends of the belt ( sensor1 and sensor2). The movement of the belt is controlled by a PLC program. The model shows a speed-controlled belt drive ( beltDrive1 and drive1) for the transport of boxes ( load2 and contact1). On/Off Switch - Failure of Sensor2 (belt end)Įnable/Disable failure of Sensor1 (belt start)Įnable/Disable failure of Sensor2 (belt end)įigure 1: Diagram view of the example model On/Off Switch - Failure of Sensor1 (belt start) Most of the elements were combined into compounds, the following are included: sensor1 The example model was created from elements of various SimulationX libraries. Starting point of this tutorial is an example model including suitable PLC programs as Step 7 projects.

#Simatic step 7 speed calculation block software
Advantages are less time-consuming and thus shorter projects, faster starts of critical operating states, the reduction of costs, parallel work due to multiple simulations of the plant, the preservation of the model beyond the delivery and a higher software quality before commissioning the plant. This model-based test approach allows for program development to start much earlier in the course of the project, since the model replaces a required automation object.
#Simatic step 7 speed calculation block verification
The focus of these tests lies on the verification of the pure program code. With the help of the interfaces used here, you are able to perform Software-in-the-Loop (SiL) tests. In the SimulationX settings under Libraries, the library InterfacesGeneral must be selected and loaded. The SimulationX installation must be performed with the option Libraries enabled. For co-simulations with Siemens S7-PLCSIM Advanced, S7-PLCSIM Advanced must be started with administrator rights, otherwise the license check with the Siemens Automation License Manager fails. both with or without administrator rights). Co-simulation with Siemens S7-PLCSIM V5.x and SimulationX must be executed under the same user name and with the same rights (e.g. For SimulationX, you also require an additional license for the module Virtual Commissioning. To perform this tutorial, you need executable installations of ESI SimulationX Professional Edition, Siemens Step 7 Professional, Siemens S7-PLCSIM V5.x and/or Siemens S7-PLCSIM Advanced V2.0 (or higher). It is als helpful if you have experience with the Siemens Step 7 and S7-PLCSIM software.
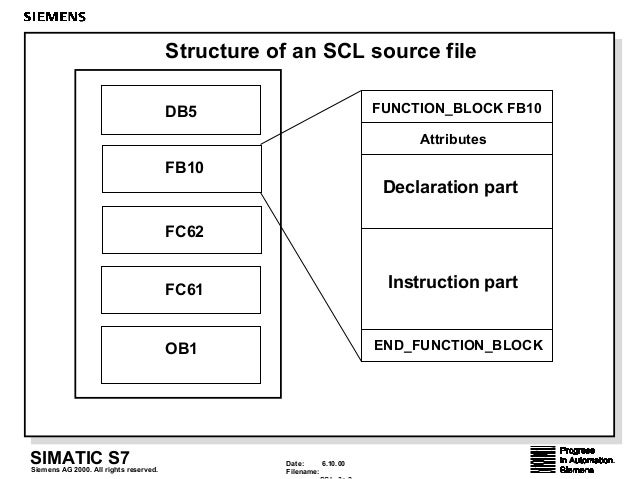
#Simatic step 7 speed calculation block how to
A general introduction on how to select elements from the libraries, how to connect these elements, how to change parameters and how to run a simulation and generate result windows can be found the tutorial Getting Started. This tutorial requires that you are familiar with the basic functionality of SimulationX.
